A Guide to Gears: 7 Gears, Their Traits, and How They Work
Get into gear with this short guide on different gears, how they work, and what they’re typically used for.
Without gears, getting around wouldn’t be nearly as easy as it is. These engineering components could be called the silent heroes of our every day lives, as they go about their business inside machines that take all the credit for their hard graft.
Here is a brief overview of different types of gears and what they are used for, for any budding engineers out there, or anyone looking to brush up on their knowledge and get into gear — literally and figuratively speaking.
RELATED: MACHINE DESIGN 101: GEAR RATIOS
1. Spur gears
Spur gears are one of the most common types of gear out there. They have cylindrical pitch surfaces and belong to the parallel shaft gear group. They have a tooth line that is straight and parallel to the shaft.
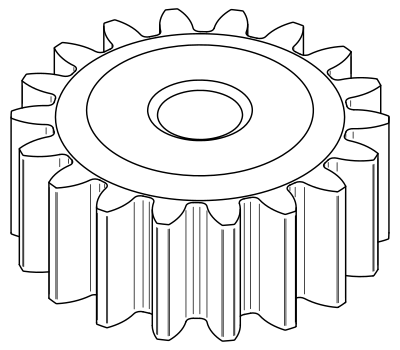
Spur gears are commonly used because they can be relatively easily produced while achieving a high performance accuracy. The larger of the meshing pair is called the gear (pictured above) and the smaller one is called the pinion. They are typically used to increase or decrease torque in machines such as washing machines, clothes dryers, screwdrivers, windup alarm clocks, and blenders.
2. Helical gears
Similarly to spur gears, helical gears are used with parallel shafts. They are also cyclindrical gears with winding tooth lines. However, they are a definite improvement in terms of design over the spur gear. Unlike spur gears the leading edges of the teeth on helical gears are not parallel to the axis of rotation — instead, they are set at an angle.

This smooth teeth meshing means that the gears can transmit higher loads and are quieter than spur gears, which can be noisy at higher speeds. As these gears create thrust force in the axial direction, they require the use of thrust bearings. They are used in machines such as elevators and in factory automation.
3. Bevel gears
Bevel gears have the appearance of a cone that has had its top cut off. Within the bevel gear family, there are several different subsets, including helical bevel gears, straight bevel gears, spiral bevel gears, and miter bevel gears.
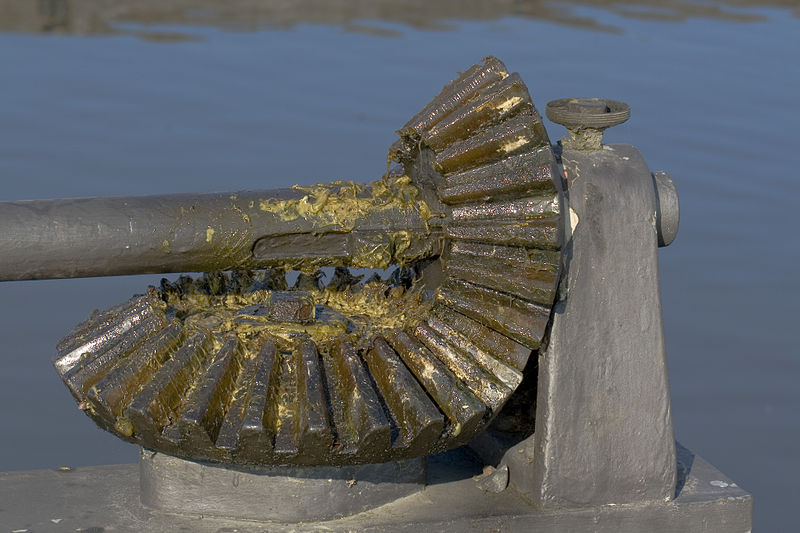
Bevel gears are used to transmit force between two shafts which intersect at a specific point. They are used in differential drives, such as those on a cornering automobile, as they can transmit power to two axles spinning at different speeds.
4. Spiral bevel gears
Spiral bevel gears are bevel gears that have curved tooth lines. Similarly to helical gears when compared to spur gears, the curvature allows for a higher tooth contact ratio, meaning that spiral bevel gears are more efficient than the standard bevel gear; they are stronger, less noisy, and vibrate less.
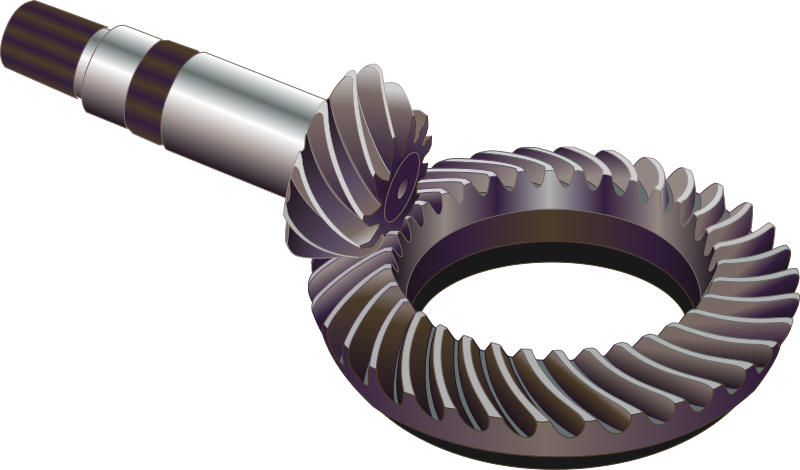
Why have spiral bevel gears not completely displaced the use of standard bevel gears you ask? Spiral bevel gears are harder to produce and, in some uses, they can also create unwanted thrust in axial directions, due to the curved teeth.
5. Worm gears
The “worm” of the worm gear refers to a screw shape cut into a shaft that the mating gear, or worm wheel, is attached to. Due to sliding contact of the gear surfaces a hard material is generally used for the worm, so as to reduce friction. Though the sliding contact means that worm gears aren’t incredibly efficient, their rotation is very smooth and quiet. As such, they are often used for industrial applications, heavy equipment, and sometimes consumer goods.

Worm gears provide very high reduction ratios and are often self-locking, as they cannot function in the reverse direction. This inherent feature makes them a safe option to use in certain types of machinery. A common example of a self-locking worm gear is the machine tuning head found on many string instruments, including the guitar.
6. Crown gears
Crown gears, also known as contrate gears, are a type of bevel gear whose teeth project at right angles to the plane of the wheel. This makes the teeth resemble the points of a crown, giving the gear its name. Unlike conical bevel gears, crown gears are cylindrical. They can either be paired with other bevel gears or spur gears, depending on the tooth design.
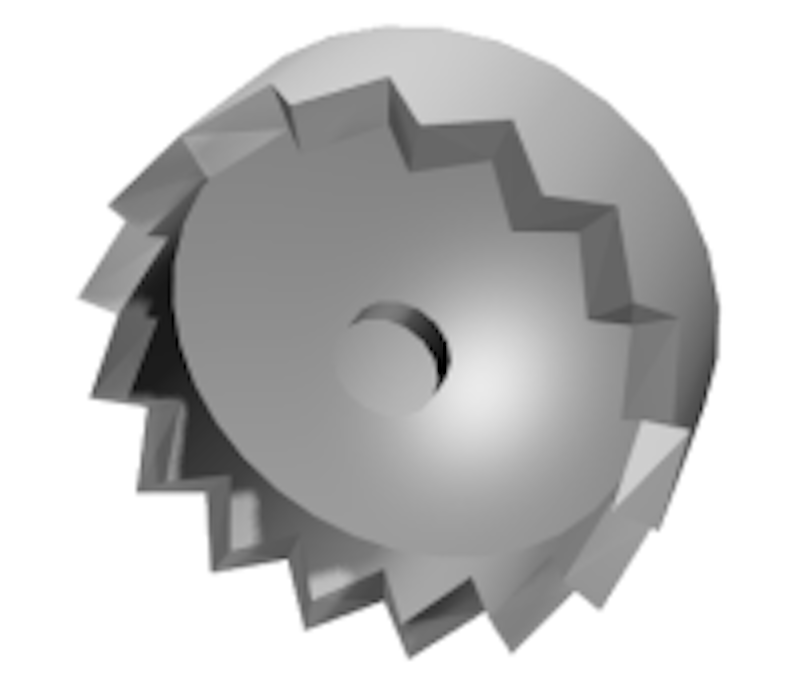
Crown gears are typically used for applications where low noise-emitting gears are required. A crown gear used with a rack‘s interlocking clogs allows the gear to roll along with the rack even if it has to go uphill or sideways. They are used for trains on uphill tracks, rollercoasters, locking doors on tracks, and car steering wheels.
7. Sun and planet gears
We probably don’t have to tell you why the sun and planet gear is called the way it is. The motion of its orbit-imitating flywheel allows the sun and planet gear to convert reciprocating motion into rotary motion. That’s why James Watt used it in his early steam engines.

In the illustration above, the sun is yellow, the planet is red, while the reciprocating arm is blue, the flywheel is green and the driveshaft gray. Sun and planet gears are an example of epicyclic gearing, or planet gearing, in which the center of one gear revolves around the center of another. They are used on anything from pencil sharpeners to locomotive engines.